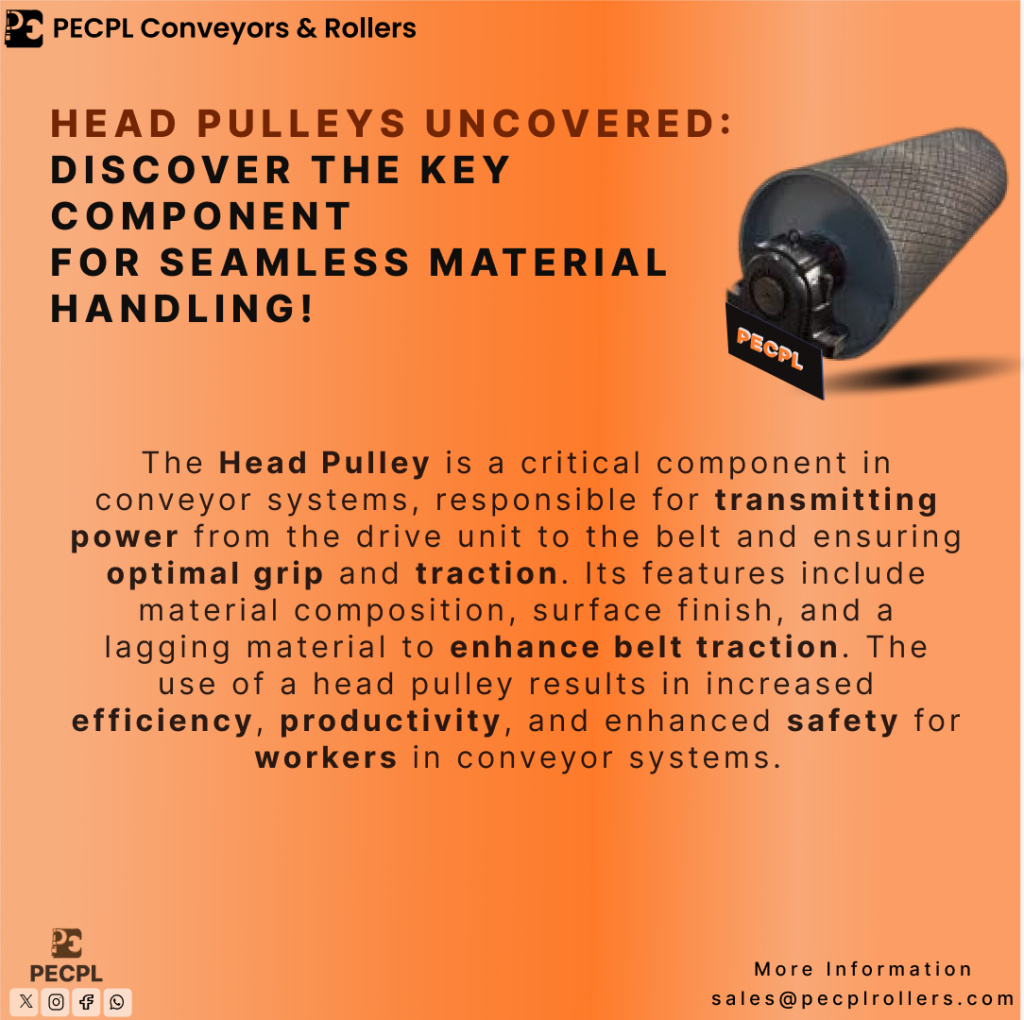
Welcome to our comprehensive guide on head pulleys – the indispensable components of conveyor systems. Whether you’re an industry professional or simply curious about this vital machinery, this article has got you covered.In this in-depth guide, we will delve into everything you need to know about head pulleys: from their purpose and types to their benefits and maintenance. So, let’s get started!
A head pulley, also known as a drive pulley, is responsible for driving the conveyor belt and moving materials from one point to another. It’s essential for smooth and efficient operation, ensuring the continuous flow of goods in various industries, including mining, manufacturing, and agriculture.Within this guide, we will explore the different types of head pulleys available, such as rubber lagged, ceramic lagged, and magnetic head pulleys, along with their respective advantages and applications. We will also provide valuable insights into their maintenance requirements to maximize their lifespan and optimize performance.
Stay tuned as we unlock the secrets to choosing the right head pulley for your needs and ensuring seamless conveyor operations throughout your facility. Let’s dive in!
What is a head pulley and what is its purpose?
A head pulley, also known as a drive pulley, is responsible for driving the conveyor belt and moving materials from one point to another. It’s essential for smooth and efficient operation, ensuring the continuous flow of goods in various industries, including mining, manufacturing, and agriculture.The primary purpose of a head pulley is to transfer power from the conveyor’s motor to the belt, allowing it to move materials along the conveyor system. This motion is achieved through the friction between the pulley’s surface and the belt. The larger the diameter of the head pulley, the greater the belt’s surface area in contact with it, resulting in increased power transmission and efficiency.In addition to power transmission, head pulleys also play a crucial role in belt tracking, as they help align the belt and prevent it from slipping or wandering off the conveyor. Proper alignment ensures optimal performance and prevents unnecessary wear and tear on the belt and pulley system.
Types of head pulleys
Head pulleys come in various types, each designed to suit specific applications and material handling needs. Understanding the different types can help you choose the most suitable head pulley for your conveyor system. Let’s explore some common types:
1. Rubber Lagged Head Pulleys
Rubber lagging is a popular choice for head pulleys due to its excellent traction and durability. The rubber coating on the pulley’s surface provides increased friction, reducing slippage and enhancing power transmission. Rubber lagging also helps protect the pulley from abrasion and extends its lifespan.Rubber lagged head pulleys are commonly used in applications where the conveyed material has a high coefficient of friction, such as bulk material handling and incline conveyors. They are also suitable for environments with high moisture or dust levels, as the rubber coating helps prevent material buildup.
2. Ceramic Lagged Head Pulleys
Ceramic lagging offers superior abrasion resistance and is particularly suitable for handling abrasive materials, such as ores, sand, and gravel. The ceramic tiles embedded in the pulley’s surface provide a hard and smooth contact point with the belt, minimizing wear and extending the pulley’s life.This type of head pulley is ideal for applications where traditional rubber lagging may wear out quickly or fail to provide sufficient traction. Ceramic lagged head pulleys are commonly used in mining operations, where durability and reliability are paramount.
3. Magnetic Head Pulleys
Magnetic head pulleys are designed to separate ferrous materials from non-magnetic materials during the material handling process. These pulleys are equipped with powerful magnets that attract and hold ferrous materials, allowing them to be easily removed from the conveyor stream.Magnetic head pulleys are commonly used in recycling facilities, where they help separate metal contaminants from recyclable materials. They are also utilized in industries such as mining and aggregate processing, where the removal of tramp metal is essential to protect downstream equipment.
The choice of head pulley type depends on the specific requirements of your application, including the type of material being conveyed, environmental conditions, and desired performance characteristics. Consulting with industry experts can help you determine the most suitable head pulley for your needs.
Components of a head pulley system
A head pulley system consists of several components that work together to ensure smooth and efficient conveyor operation. Understanding these components is essential for proper installation, maintenance, and troubleshooting. Let’s take a closer look at each component:
1. Head Pulley
The head pulley itself is the main component of the system, responsible for driving the conveyor belt and moving materials. It is typically located at the discharge end of the conveyor and is directly connected to the motor or drive unit.Head pulleys are usually cylindrical in shape, with a smooth or lagged surface, depending on the specific type. They are available in various diameters and widths to accommodate different belt sizes and material handling capacities.
2. Drive Unit
The drive unit consists of an electric motor, gearbox, and couplings, and is responsible for providing power to the head pulley. The motor converts electrical energy into mechanical energy, which is transmitted to the pulley through the gearbox and couplings.The drive unit’s power and speed requirements depend on the conveyor system’s load capacity, material characteristics, and desired throughput. Proper selection of the drive unit ensures optimal performance and prevents overloading or underutilization of the conveyor system.
3. Belt
The conveyor belt is an integral part of the head pulley system, as it carries the materials from one point to another. It is made of multiple layers of rubber or fabric, designed to withstand the stresses of material handling and maintain proper tension.The belt’s width and thickness depend on the application and material handling requirements. It is essential to choose the right belt type and ensure proper tensioning to prevent slippage and premature wear.
4. Belt Cleaner
A belt cleaner is used to remove material residue, such as dust, fines, or carryback, from the conveyor belt’s surface. This helps maintain belt cleanliness, prevent material buildup, and ensure efficient operation.Belt cleaners can be either primary or secondary, depending on their position relative to the head pulley. Primary cleaners are installed close to the head pulley and are responsible for the initial removal of bulk material. Secondary cleaners are positioned further downstream and provide additional cleaning and fine-tuning.
5. Belt Tracking System
Proper alignment and tracking of the conveyor belt are crucial for the smooth and reliable operation of the head pulley system. A belt tracking system consists of various components, such as tracking rollers, training idlers, and guide strips, that help keep the belt centered and prevent lateral movement.A misaligned belt can cause premature wear on the pulley and belt edges, leading to increased maintenance and downtime. Regular inspection and adjustment of the belt tracking system are necessary to ensure optimal performance and minimize the risk of belt damage.
Understanding the components of a head pulley system is essential for proper installation, maintenance, and troubleshooting. Regular inspection and maintenance of these components can help identify and resolve issues before they escalate, ensuring the longevity and efficiency of the conveyor system.
Importance of proper head pulley maintenance
Maintaining head pulleys is crucial for maximizing their lifespan and optimizing conveyor system performance. Regular maintenance not only prevents costly breakdowns but also ensures the safety of personnel working with the equipment. Here are some key reasons why proper head pulley maintenance is essential:
1. Preventing Belt Slippage
Belt slippage is a common issue in conveyor systems and can result in reduced conveying capacity, increased power consumption, and premature wear on the belt and pulley. Regular maintenance, including cleaning, inspection, and proper tensioning, helps prevent belt slippage and maintains optimal power transmission.
2. Extending Pulley Life
Head pulleys are subjected to constant wear and tear due to the friction and forces involved in material handling. Regular maintenance, such as cleaning, lubrication, and lagging replacement, helps extend the pulley’s life and reduces the need for costly replacements.
3. Ensuring Belt Alignment
Proper alignment of the conveyor belt is critical for smooth operation and prevents unnecessary wear on the belt and pulley. Regular inspection and adjustment of the belt tracking system, including tracking rollers and guide strips, help ensure optimal belt alignment and minimize the risk of misalignment-related issues.
4. Minimizing Downtime
Unplanned downtime due to head pulley failure can be costly and disrupt production schedules. Regular maintenance, including inspections and timely repairs, helps identify and address potential issues before they escalate into major problems, minimizing the risk of unexpected downtime.
5. Ensuring Safety
Safety should always be a top priority when working with conveyor systems and head pulleys. Regular maintenance helps identify and rectify potential safety hazards, such as loose parts, damaged components, or inadequate guarding, ensuring a safe working environment for personnel.Proper head pulley maintenance involves a combination of routine inspections, cleaning, lubrication, and timely repairs. Following manufacturer guidelines and consulting with industry experts can help establish an effective maintenance schedule tailored to your specific conveyor system.
Common issues and troubleshooting for head pulleys
Despite regular maintenance, head pulleys may encounter various issues that can affect their performance and the overall conveyor system. Understanding these issues and knowing how to troubleshoot them can help minimize downtime and reduce the risk of costly repairs. Let’s explore some common issues and their troubleshooting methods:
1. Belt Slippage
Belt slippage occurs when the conveyor belt fails to grip the head pulley properly, resulting in reduced conveying capacity and increased power consumption. Possible causes of belt slippage include inadequate tension, worn-out lagging, or excessive material buildup.
To troubleshoot belt slippage, start by checking the belt tension and adjusting it if necessary. Ensure that the lagging surface is clean and free from debris or material buildup. If the lagging is worn out or damaged, consider replacing it to restore proper grip and power transmission.
2. Belt Misalignment
Belt misalignment can lead to premature wear on the belt edges, increased maintenance, and reduced conveyor performance. Misalignment can occur due to improper installation, worn-out or damaged tracking rollers, or excessive material buildup on the belt.
To troubleshoot belt misalignment, start by inspecting the tracking rollers and guide strips for wear or damage. Replace any worn-out or damaged components and ensure that the tracking system is properly aligned and adjusted. Regular cleaning and removal of material buildup from the belt can also help prevent misalignment.
3. Excessive Noise or Vibration
Excessive noise or vibration from the head pulley system can indicate underlying issues, such as misalignment, loose components, or worn-out bearings. Ignoring these symptoms can lead to further damage and increased maintenance requirements.
To troubleshoot excessive noise or vibration, start by inspecting the head pulley for signs of misalignment or loose components. Check the bearings for wear or damage and lubricate them if necessary. If the issue persists, consult with a qualified technician to identify and address the underlying cause.
4. Material Buildup on Pulley Surface
Material buildup on the head pulley surface can affect its performance and lead to belt slippage or misalignment. Excessive material buildup can be caused by factors such as improper belt cleaning, inadequate belt tension, or the characteristics of the conveyed material.
To troubleshoot material buildup, ensure that the belt cleaning system is functioning correctly and removing debris effectively. Adjust the belt tension if necessary to prevent material from sticking to the pulley surface. If the conveyed material is prone to sticking or causing buildup, consider using a different type of head pulley or implementing additional cleaning measures.
5. Premature Lagging Wear
Premature wear of the pulley lagging can reduce its effectiveness and lead to decreased power transmission and increased maintenance costs. Factors that can contribute to premature lagging wear include excessive belt tension, abrasive materials, or inadequate lagging quality.
To troubleshoot premature lagging wear, evaluate the belt tension and adjust it to the manufacturer’s recommendations. If the conveyed material is highly abrasive, consider using a more durable lagging material, such as ceramic. Regular inspection and cleaning of the lagging surface can also help identify signs of wear and take timely action.
Proper troubleshooting requires a systematic approach, starting with a thorough inspection and identification of the underlying cause. Consultation with industry experts or qualified technicians can provide valuable insights and guidance in resolving head pulley issues effectively.
Choosing the right head pulley for your application
Selecting the right head pulley for your application is crucial for ensuring optimal performance, longevity, and cost-effectiveness. Factors such as material characteristics, conveyor system design, and operating conditions should be taken into consideration when making this decision. Here are some key considerations to keep in mind:
1. Material Characteristics
The type of material being conveyed plays a significant role in determining the most suitable head pulley. For example, if the material is highly abrasive, a ceramic lagged head pulley may be the best choice to withstand the wear. If the material is prone to sticking or causing buildup, a rubber lagged head pulley with effective cleaning measures may be recommended.Consider the size, shape, weight, and temperature of the material, as these factors can influence the selection of the head pulley. Consulting with material handling experts or head pulley manufacturers can provide valuable insights into the optimal choice for your specific material characteristics.
2. Conveyor System Design
The design of your conveyor system, including its length, width, and capacity, should be taken into account when selecting a head pulley. The head pulley’s diameter and width should match the belt size and capacity requirements to ensure proper power transmission and minimize belt slippage.Consider the overall layout of your conveyor system, including any inclines or declines, as these factors can affect the required grip and power transmission of the head pulley. The head pulley should be able to handle the anticipated load and provide sufficient traction for smooth operation.
3. Operating Conditions
The operating conditions of your facility, such as temperature, moisture levels, and environmental factors, can influence the choice of head pulley. For example, if your facility operates in high moisture or corrosive environments, a head pulley with corrosion-resistant properties may be necessary.Consider any specific safety requirements or regulations that apply to your industry or facility. Some industries, such as food processing or pharmaceuticals, may require head pulleys that meet specific hygiene or contamination control standards.
4. Budget and Long-Term Costs
While cost should never be the sole determining factor, it is an important consideration when choosing a head pulley. Evaluate the initial cost, maintenance requirements, and expected lifespan of different head pulley options to determine the most cost-effective choice for your application.Consider the long-term costs associated with maintenance, repairs, and downtime. Investing in a higher-quality head pulley upfront may result in lower overall costs over its lifespan, compared to a cheaper option that requires frequent replacement or repairs.
Consulting with head pulley manufacturers, industry experts, or material handling consultants can help
Installation and alignment of head pulleys
A head pulley, also known as a drive pulley, is responsible for driving the conveyor belt and moving materials from one point to another. It’s essential for smooth and efficient operation, ensuring the continuous flow of goods in various industries, including mining, manufacturing, and agriculture.
When it comes to choosing the right head pulley for your application, several factors need to be considered. The first step is to determine the specific requirements of your conveyor system. This includes understanding the type and weight of materials being transported, the speed and capacity requirements, and any environmental conditions that may affect the pulley’s performance.Next, you need to consider the type of head pulley that best suits your needs. There are different types available, each with its own advantages and applications. Rubber lagged head pulleys, for example, provide excellent grip and traction, making them ideal for handling bulk materials. On the other hand, ceramic lagged head pulleys offer exceptional durability and resistance to wear, making them suitable for abrasive materials.
Magnetic head pulleys, as the name suggests, utilize powerful magnets to attract and separate ferrous materials from the rest of the conveyed material. This type of pulley is commonly used in recycling and waste management industries where the removal of metal contaminants is crucial.In addition to considering the type of head pulley, it’s important to select the appropriate diameter and face width. The diameter determines the belt’s wrap angle, affecting the pulley’s gripping ability. The face width, on the other hand, determines the contact area between the belt and pulley, influencing the belt’s tracking and overall performance.
Properly selecting the right head pulley for your application is essential to ensure optimal conveyor performance and longevity. By taking into account the specific requirements of your system and choosing the appropriate type, diameter, and face width, you can maximize efficiency and minimize downtime.
Safety considerations for working with head pulleys
Once you have selected the right head pulley for your application, proper installation and alignment are crucial to ensure its smooth operation. Improper installation can lead to premature wear, belt tracking issues, and even safety hazards. Therefore, it’s important to follow certain guidelines to ensure a successful installation.Before installing the head pulley, it’s necessary to inspect the conveyor system, including the belt, idlers, and other components, to identify any potential issues or damage that may affect the pulley’s performance. It’s also important to ensure that all necessary safety precautions are taken, such as locking out power sources and using appropriate personal protective equipment.
During the installation process, proper alignment of the head pulley is essential. Misalignment can cause excessive belt wear, tracking problems, and increased power consumption. To achieve proper alignment, it’s recommended to use precision tools, such as laser alignment systems, to ensure accurate positioning of the pulley.Additionally, it’s important to properly tension the belt to prevent slippage and ensure efficient power transmission. This can be achieved by following the manufacturer’s guidelines and using appropriate tensioning devices, such as belt tensioners or take-up systems.
Regular maintenance and inspection are also crucial to ensure the continued performance of the head pulley. This includes checking for any signs of wear, damage, or misalignment and addressing them promptly to prevent further complications. Lubrication of bearings and other moving parts should also be performed as per the manufacturer’s recommendations.By following these installation and alignment guidelines and implementing a regular maintenance routine, you can ensure the longevity and optimal performance of your head pulley, contributing to the overall efficiency of your conveyor system.
Conclusion and final thoughts
While head pulleys play a vital role in conveyor systems, it’s important to prioritize safety when working with these components. Failure to adhere to safety guidelines can result in serious injuries or accidents. Therefore, it’s crucial to implement appropriate safety measures to protect workers and maintain a safe working environment.One of the key safety considerations when working with head pulleys is proper lockout/tagout procedures. Before performing any maintenance or repair work, it’s essential to de-energize the conveyor system and lockout/tagout the power sources to prevent accidental startup. This ensures that the pulley and other moving parts cannot be activated while work is being carried out.Additionally, it’s important to provide adequate training and education to workers regarding the potential hazards associated with head pulleys and the necessary precautions to be taken. This includes proper use of personal protective equipment, such as gloves and safety glasses, as well as awareness of pinch points and other potential dangers.Regular inspections of the conveyor system should also be conducted to identify any safety hazards or maintenance issues that may arise. Any identified issues should be addressed promptly to prevent accidents or equipment failures.
By prioritizing safety and implementing appropriate safety measures, you can create a safe working environment and minimize the risk of accidents or injuries when working with head pulleys.